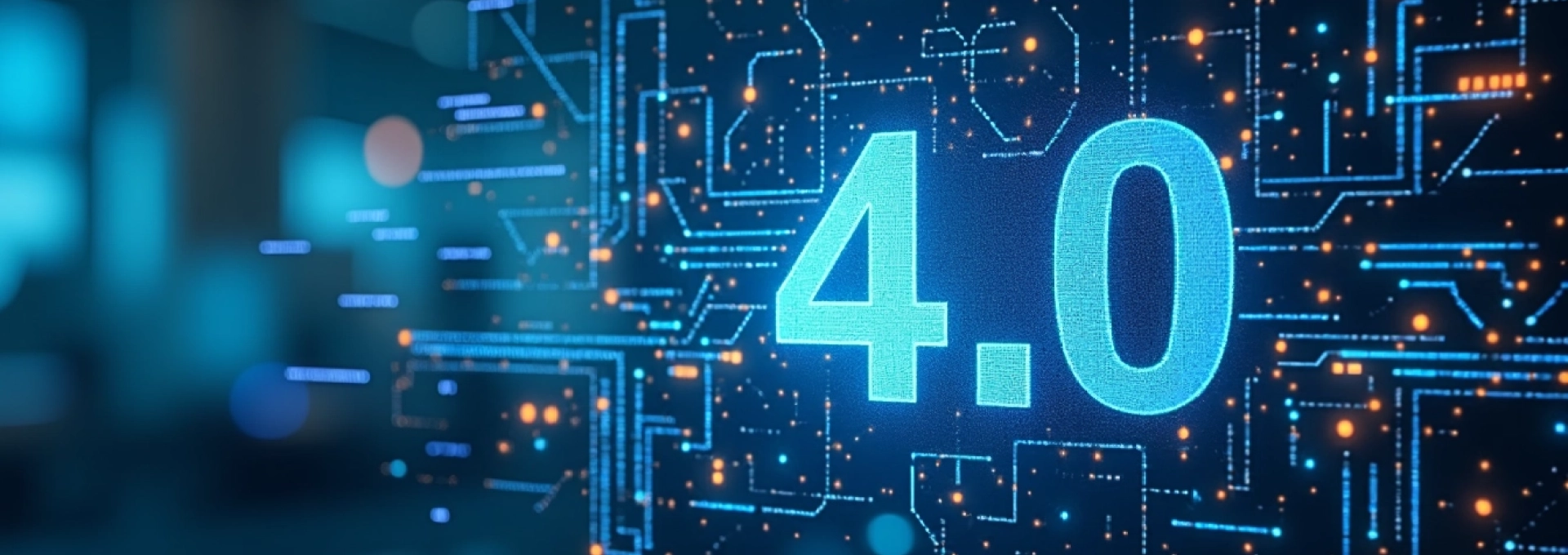
Le revamping industriel s'impose comme une stratégie incontournable pour les entreprises désireuses de rester compétitives dans un environnement économique en constante évolution. Cette approche de modernisation globale permet aux industries de transformer leurs installations existantes pour répondre aux défis actuels et futurs. En alliant innovation technologique et optimisation des processus, le revamping offre une solution sur mesure pour accroître la productivité, réduire les coûts et améliorer la qualité des produits. Face à la pression concurrentielle et aux exigences réglementaires croissantes, de plus en plus d'entreprises se tournent vers cette démarche pour donner un nouveau souffle à leur outil industriel.
Optimisation des processus de production par le revamping
L'optimisation des processus de production est au cœur du revamping industriel. Cette démarche vise à repenser l'ensemble de la chaîne de production pour éliminer les goulots d'étranglement, réduire les temps d'arrêt et maximiser l'efficacité opérationnelle. En analysant en profondeur chaque étape du processus, les entreprises peuvent identifier les opportunités d'amélioration et mettre en place des solutions innovantes.
L'un des aspects clés de cette optimisation est la réduction des temps de cycle. En modernisant les équipements et en intégrant des technologies de pointe, il est possible de diminuer significativement le temps nécessaire à la fabrication d'un produit. Cela se traduit par une augmentation de la capacité de production sans nécessairement augmenter les ressources.
Un autre avantage majeur du revamping est la flexibilité accrue qu'il apporte aux lignes de production. Dans un contexte où les demandes du marché évoluent rapidement, la capacité à s'adapter rapidement à de nouveaux produits ou à des volumes de production variables est cruciale. Le revamping permet de concevoir des lignes de production modulaires et reconfigurables, offrant ainsi une plus grande agilité face aux fluctuations du marché.
La réduction des pertes et des rebuts est également un objectif important du revamping. En intégrant des systèmes de contrôle qualité avancés et en optimisant les paramètres de production, les entreprises peuvent significativement améliorer leur taux de rendement synthétique (TRS) et réduire les coûts liés aux défauts de fabrication.
Modernisation des équipements et systèmes industriels
La modernisation des équipements et systèmes industriels constitue un pilier essentiel du revamping. Cette étape cruciale permet aux entreprises de se doter d'outils de production à la pointe de la technologie, capables de répondre aux exigences actuelles du marché. Le novae-group.com propose des solutions de retrofit qui s'inscrivent parfaitement dans cette démarche de modernisation.
L'un des aspects les plus significatifs de cette modernisation est l'amélioration de la précision et de la répétabilité des processus. Les équipements modernes, dotés de capteurs avancés et de systèmes de contrôle sophistiqués, permettent d'atteindre des niveaux de précision inégalés. Cela se traduit par une qualité de produit supérieure et une réduction des variations dans la production.
Intégration de l'automatisation avancée et de l'industrie 4.0
L'intégration de l'automatisation avancée et des concepts de l'industrie 4.0 est un élément clé du revamping industriel moderne. Cette approche permet aux entreprises de tirer pleinement parti des technologies numériques pour optimiser leurs opérations. L'automatisation intelligente, basée sur l'intelligence artificielle et l'apprentissage automatique, offre de nouvelles possibilités pour améliorer la productivité et la qualité.
Les robots collaboratifs, ou cobots, représentent une avancée majeure dans ce domaine. Ils permettent une interaction sûre et efficace entre les opérateurs humains et les machines, ouvrant la voie à de nouveaux modèles de production flexibles et adaptables. L'intégration de ces technologies dans le cadre d'un revamping peut considérablement améliorer l'ergonomie des postes de travail et réduire les risques de troubles musculo-squelettiques chez les opérateurs.
Mise à niveau des systèmes de contrôle-commande (SCADA, DCS)
La mise à niveau des systèmes de contrôle-commande est un aspect crucial du revamping industriel. Les systèmes SCADA (Supervisory Control and Data Acquisition) et DCS (Distributed Control System) modernes offrent des capacités de surveillance et de contrôle en temps réel qui dépassent largement celles des systèmes plus anciens. Cette modernisation permet une gestion plus fine et plus réactive des processus industriels.
L'intégration de ces systèmes avancés facilite la collecte et l'analyse de données opérationnelles en temps réel. Cela permet aux entreprises de prendre des décisions éclairées plus rapidement et d'optimiser continuellement leurs processus. Par exemple, un système SCADA moderne peut détecter des anomalies subtiles dans le fonctionnement des équipements bien avant qu'elles ne deviennent des problèmes majeurs, permettant ainsi une maintenance prédictive efficace.
Remplacement des machines obsolètes par des technologies de pointe
Le remplacement des machines obsolètes par des technologies de pointe est souvent au cœur des projets de revamping. Ces nouvelles machines offrent généralement une meilleure efficacité énergétique, une plus grande précision et une capacité de production accrue. Par exemple, le remplacement d'anciennes presses hydrauliques par des modèles électriques de dernière génération peut entraîner une réduction significative de la consommation d'énergie tout en améliorant la qualité et la cadence de production.
L'intégration de machines à commande numérique (CNC) avancées est un autre exemple de modernisation qui peut transformer radicalement les capacités de production d'une entreprise. Ces machines offrent une flexibilité et une précision inégalées, permettant la fabrication de pièces complexes avec une efficacité remarquable.
Amélioration de l'efficacité énergétique des installations
L'amélioration de l'efficacité énergétique est un objectif majeur de nombreux projets de revamping industriel. Dans un contexte où les coûts énergétiques ne cessent d'augmenter et où les réglementations environnementales se durcissent, optimiser la consommation d'énergie devient une priorité pour de nombreuses entreprises.
Le revamping offre l'opportunité d'intégrer des technologies écoénergétiques à tous les niveaux de l'installation industrielle. Cela peut inclure l'installation de moteurs à haut rendement, la mise en place de systèmes de récupération de chaleur, ou encore l'optimisation des systèmes d'éclairage et de climatisation. Par exemple, le remplacement d'anciens compresseurs d'air par des modèles modernes à vitesse variable peut entraîner des économies d'énergie allant jusqu'à 30%.
Conformité réglementaire et sécurité industrielle renforcée
La conformité réglementaire et le renforcement de la sécurité industrielle sont des aspects cruciaux du revamping. Dans un environnement réglementaire de plus en plus strict, les entreprises doivent constamment s'adapter pour rester en conformité avec les normes en vigueur. Le revamping offre l'opportunité de mettre à niveau les installations pour répondre à ces exigences tout en améliorant la sécurité globale des opérations.
Mise en conformité avec les normes ISO 45001 et OHSAS 18001
La mise en conformité avec les normes ISO 45001 et OHSAS 18001 est un objectif important pour de nombreuses entreprises engagées dans un processus de revamping. Ces normes internationales définissent les exigences pour un système de management de la santé et de la sécurité au travail efficace. Le revamping permet d'intégrer ces exigences dès la conception des nouveaux processus et équipements.
Par exemple, l'installation de systèmes de ventilation améliorés ou la mise en place de zones de travail ergonomiques peuvent contribuer significativement à la conformité avec ces normes. De plus, l'intégration de systèmes de surveillance avancés permet un meilleur suivi des indicateurs de santé et de sécurité, facilitant ainsi la gestion continue de la conformité.
Implémentation de systèmes de sécurité machine selon EN ISO 13849
L'implémentation de systèmes de sécurité machine conformes à la norme EN ISO 13849 est un aspect crucial du revamping industriel. Cette norme définit les exigences de sécurité pour les systèmes de commande des machines. Dans le cadre d'un revamping, cela peut impliquer l'installation de nouveaux dispositifs de sécurité tels que des barrières immatérielles, des tapis de sécurité ou des systèmes d'arrêt d'urgence avancés.
L'intégration de ces systèmes de sécurité modernes permet non seulement d'améliorer la protection des opérateurs, mais aussi d'optimiser la productivité en réduisant les temps d'arrêt liés aux incidents de sécurité. Par exemple, l'utilisation de scanners laser de sécurité peut permettre une interaction plus fluide entre les opérateurs et les machines tout en garantissant un niveau de sécurité élevé.
Réduction des risques industriels et prévention des accidents
La réduction des risques industriels et la prévention des accidents sont des objectifs fondamentaux du revamping. Cette démarche permet de repenser l'ensemble des processus et des équipements sous l'angle de la sécurité, en intégrant les dernières avancées technologiques en matière de prévention des risques.
L'utilisation de l'analyse des risques assistée par ordinateur ( HAZOP
) et de la modélisation 3D des installations permet d'identifier et de traiter les risques potentiels dès la phase de conception. De plus, l'intégration de systèmes de détection précoce des anomalies, comme les capteurs de gaz ou les caméras thermiques, contribue à prévenir les incidents avant qu'ils ne se produisent.
Augmentation de la compétitivité et de la rentabilité
L'augmentation de la compétitivité et de la rentabilité est souvent le principal moteur des projets de revamping industriel. En modernisant leurs installations, les entreprises peuvent significativement améliorer leur position concurrentielle sur le marché tout en optimisant leur structure de coûts.
Réduction des coûts opérationnels et de maintenance
La réduction des coûts opérationnels et de maintenance est l'un des avantages les plus tangibles du revamping industriel. Les équipements modernes sont généralement plus fiables et nécessitent moins d'interventions de maintenance, ce qui se traduit par une réduction des temps d'arrêt et des coûts associés.
L'introduction de technologies de maintenance prédictive, telles que l'analyse vibratoire ou la thermographie, permet d'anticiper les pannes et d'optimiser les interventions de maintenance. Cela peut conduire à une réduction significative des coûts de maintenance, pouvant atteindre 30% dans certains cas.
Amélioration de la qualité produit et réduction des non-conformités
L'amélioration de la qualité des produits et la réduction des non-conformités sont des objectifs clés du revamping industriel. Les équipements modernes, dotés de systèmes de contrôle avancés, permettent une meilleure maîtrise des paramètres de production, ce qui se traduit par une qualité plus constante et une réduction des défauts.
L'intégration de systèmes de contrôle qualité en ligne, utilisant des technologies telles que la vision artificielle ou l'analyse spectrale, permet de détecter et de corriger les défauts en temps réel. Cela peut conduire à une réduction significative des taux de rebut et des coûts associés aux non-conformités.
Flexibilité accrue face aux variations de la demande du marché
La flexibilité accrue face aux variations de la demande du marché est un avantage compétitif majeur offert par le revamping industriel. Les lignes de production modernisées sont généralement plus adaptables et peuvent être reconfigurées rapidement pour s'adapter à de nouveaux produits ou à des volumes de production variables.
L'utilisation de technologies telles que les systèmes de production flexibles (FMS) ou les cellules de fabrication reconfigurables permet aux entreprises de répondre plus rapidement aux changements de la demande du marché. Cette agilité peut se traduire par une réduction des délais de mise sur le marché de nouveaux produits et une meilleure capacité à saisir les opportunités commerciales.
Transformation digitale et gestion des données industrielles
La transformation digitale et la gestion efficace des données industrielles sont devenues des enjeux majeurs pour les entreprises engagées dans un processus de revamping. L'intégration de technologies numériques avancées permet non seulement d'optimiser les processus de production, mais aussi de tirer parti de la richesse des données générées par les équipements industriels.
Déploiement de l'IIoT (Industrial Internet Of Things) et des capteurs intelligents
Le déploiement de l'Internet Industriel des Objets (IIoT) et des capteurs intelligents est un aspect clé de la transformation digitale dans le cadre du revamping industriel. Ces technologies permettent de collecter en temps réel une multitude de données sur le fonctionnement des équipements et les processus de production.
L'utilisation de capteurs MEMS
(Micro-Electro-Mechanical Systems) avancés, par exemple, permet de surveiller avec une grande précision des paramètres tels que la température, la pression, les vibrations ou la qualité de l'air. Ces données, transmises via des réseaux sans fil sécurisés, permettant une analyse en temps réel des performances des équipements et l'identification précoce des anomalies. Cette approche facilite la mise en place de stratégies de maintenance prédictive, réduisant ainsi les temps d'arrêt imprévus et les coûts associés.
L'intégration de l'IIoT permet également une meilleure traçabilité des produits tout au long de la chaîne de production. Par exemple, l'utilisation de tags RFID ou de codes QR intelligents peut permettre de suivre chaque produit individuellement, facilitant ainsi la gestion de la qualité et la réponse aux exigences réglementaires.
Implémentation de solutions MES (Manufacturing Execution System)
L'implémentation de solutions MES (Manufacturing Execution System) est une étape cruciale dans la transformation digitale des entreprises industrielles. Ces systèmes agissent comme un pont entre les systèmes de planification de l'entreprise (ERP) et les systèmes de contrôle au niveau de l'atelier, offrant une visibilité en temps réel sur l'ensemble des opérations de production.
Un MES moderne permet d'optimiser la planification de la production, de suivre la progression des ordres de fabrication, et de collecter des données détaillées sur les performances des équipements. Par exemple, l'intégration d'un MES peut permettre de réduire les temps de changement de série jusqu'à 30% en optimisant la séquence des opérations et en fournissant des instructions précises aux opérateurs.
De plus, les solutions MES facilitent la mise en place de systèmes de contrôle qualité intégrés, permettant de détecter et de corriger rapidement les écarts par rapport aux spécifications. Cela se traduit par une réduction significative des coûts liés à la non-qualité et une amélioration de la satisfaction client.
Analyse prédictive et maintenance conditionnelle basée sur les données
L'analyse prédictive et la maintenance conditionnelle basée sur les données représentent une avancée majeure dans la gestion des équipements industriels. En exploitant les données collectées par les capteurs IoT et les systèmes MES, les entreprises peuvent anticiper les pannes et optimiser leurs interventions de maintenance.
Les algorithmes d'apprentissage automatique peuvent analyser les schémas complexes dans les données opérationnelles pour prédire avec précision quand un équipement est susceptible de tomber en panne. Par exemple, l'analyse des vibrations d'une machine tournante peut révéler des signes précoces d'usure des roulements, permettant une intervention avant que la panne ne se produise.
Cette approche peut conduire à une réduction significative des temps d'arrêt non planifiés, avec des économies pouvant atteindre 50% des coûts de maintenance dans certains cas. De plus, la maintenance conditionnelle permet d'optimiser la durée de vie des composants, en évitant les remplacements prématurés ou tardifs.
Intégration de jumeaux numériques pour l'optimisation des processus
L'intégration de jumeaux numériques représente une avancée significative dans l'optimisation des processus industriels. Un jumeau numérique est une réplique virtuelle d'un équipement ou d'un processus physique, alimentée en temps réel par les données collectées sur le terrain.
Cette technologie permet de simuler et d'optimiser les processus de production dans un environnement virtuel avant de les mettre en œuvre dans le monde réel. Par exemple, un fabricant automobile peut utiliser un jumeau numérique de sa ligne d'assemblage pour tester différentes configurations et identifier la plus efficace, sans perturber la production en cours.
Les jumeaux numériques offrent également des possibilités avancées de formation et de planification des interventions. Les opérateurs peuvent s'entraîner sur une version virtuelle de l'équipement, réduisant ainsi les risques d'erreurs lors de l'utilisation réelle. De même, les équipes de maintenance peuvent planifier et simuler des interventions complexes, optimisant ainsi leur efficacité et leur sécurité.